MANY SURFACE PREPARATION OPTIONS
From a dazzling mirror-like appearance to a totally nonreflective texture, specially prepared surface finishes add both functionality and attractiveness to many products. A matte finish is normally used on the interior of cameras, microscopes and other optical products. The front panels of many pieces of electronic equipment have a brushed or satin finish, while a number of consumer products have enhanced appeal due to their highly polished appearance. Medical and dental tools for surgery are another application where a smooth polished surface is required. More than one texture can often be utilized on a single component.
POLISHING – Both manual and automated polishing techniques are often utilized before anodizing to smooth irregularities and increase surface reflectivity. Polishing provides a highly decorative and mechanically smooth surface. A highly polished and anodized finish adds eye appeal and value to any component.


GRAINING – A grained, brushed or satin surface, plus anodizing, yields a high-tech satin look. Grained or blasted finishes are a practical method to remove surface irregularities while imparting a quality textured finish prior to applying a protective coating.
BLASTING – A variety of abrasive substances are used to break up or remove surface irregularities. It is also useful for light deburring. This technique creates a nonreflective finish, within a range of controlled textures, which may then be anodized.
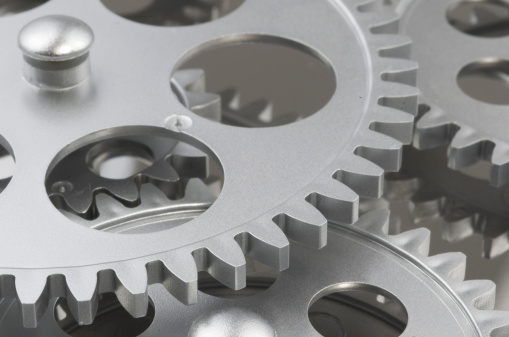
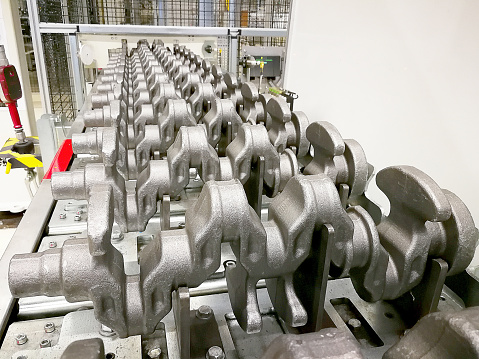
SHOT PEEN – Used to strengthen and relieve stress in components like steel automobile crankshafts and connecting rods. In architecture it provides a muted finish to metal. Shot peening is similar mechanically to sandblasting, though its purpose is not to remove material, but rather it employs the mechanism of plasticity to achieve its goal, with each particle functioning as a ball-peen hammer.
Quality Considerations During Anodizing, Contamination Caused by Deburring Wheels During Anodizing